コンプレッション成型
<例>ゴム成形金型のデータ
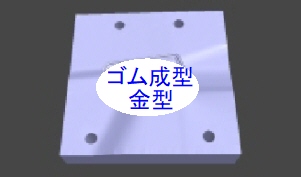
コンプレッション成型(Compression Molding)について
圧縮成形型は、熱硬化性樹脂(または一部の熱可塑性樹脂)を使用し、加熱と圧力をかけ成形する製造プロセスの一つです。 主に自動車部品、電気部品、航空宇宙材料、スポーツ用品などの製造に利用されます。
コンプレッション成型のプロセス
- 材料の準備
- 樹脂(粉末、ペレット、シート、またはプリフォーム)を適切な量で準備します。
- 一般的には熱硬化性樹脂(BMC、SMC、フェノール樹脂など)が用いられる。
- 金型への配置
- 素材を加熱された金型のキャビティに配置。
- 金型の設計によって、最終製品の形状や表面仕上げが決定される。
- 圧力をかける
- サクサクプレス機を用いて上型を押し下げ、材料を金型全体に均等に配布させます。
- 圧力は通常、数MPa(メガパスカル)から数十MPaの範囲です。
- 加熱・硬化
- 一定時間加熱(120~200℃)し、材料を硬化させます。
- 熱硬化性樹脂の場合、架橋反応により強度が高まります。
- 冷却・取り出し
- 成型品を冷却し、金型を開いて取り出す。
- 必要に応じてバリ取りや後処理を行います。
コンプレッション成型のメリット
✅コスト効率が良い(特に大量生産に適している)
✅強度が高い(熱硬化性樹脂を置くため、耐熱性・耐薬品性が優れる)
✅精密な形状を再現可能(金型次第で複雑な)形状も対応)
✅材料の無駄が少ない(適量を充填することでロスを極力抑えられる)
コンプレッション形成型の欠点
❌サイクルタイムが長い(加熱・硬化に時間がかかる)
❌形状自由度が低い(複雑な中空構造などは難しい)
❌バリや後処理が必要(金型合わせにバリが発生する可能性)
コンプレッション成型と他の成型方法の比較
成型方法 | いいね | ライン | 主な用途 |
---|---|---|---|
コンプレッション成形型 | 高強度・低コスト | サイクルタイムが長い | 自動車・電気部品 |
射出成型(射出成形) | 高精度・高速成形 | 金型コストが高い | 大量生産品 |
トランスファー成型(トランスファーモールディング) | 精密成形が可能 | 金型が複雑・コスト高 | 電子部品・精密部品 |
ブロー成型(ブロー成形) | 中空構造が可能 | 厚みの均一化が難しい | ボトル・タンク |
まとめ
圧縮成形型は、高強度・低コストで成形可能な技術であり、自動車や電気部品などに広く利用されています。 特に、熱硬化性樹脂を用いた成形に適しており、強度や耐熱性に優れています他の成形方法と比較しながら、適切な用途に応じて選択することが重要です。
<3dスキャン事例一覧> |